3D Scanner for EV Hairpin Stator Automated Inspection
ZEISS ScanBox for eMotors
Accurate Digitalization and Quality Control of Electric Motor Hairpin-Stator Assemblies
The ZEISS ScanBox for eMotors is engineered to accurately digitize electric motor hairpins and stators for fast and reliable dimensional inspection. This automated 3D scanning solution allows complete stators, including the hairpins and individual or multiple hairpins, to be digitized and inspected precisely. Visualizing the captured 3D measurement data within the ZEISS Quality Suite allows you to perform more comprehensive analysis with powerful 3D inspection software.
Automated Inspection and Digitalization of EV Motor Hairpins and Stators
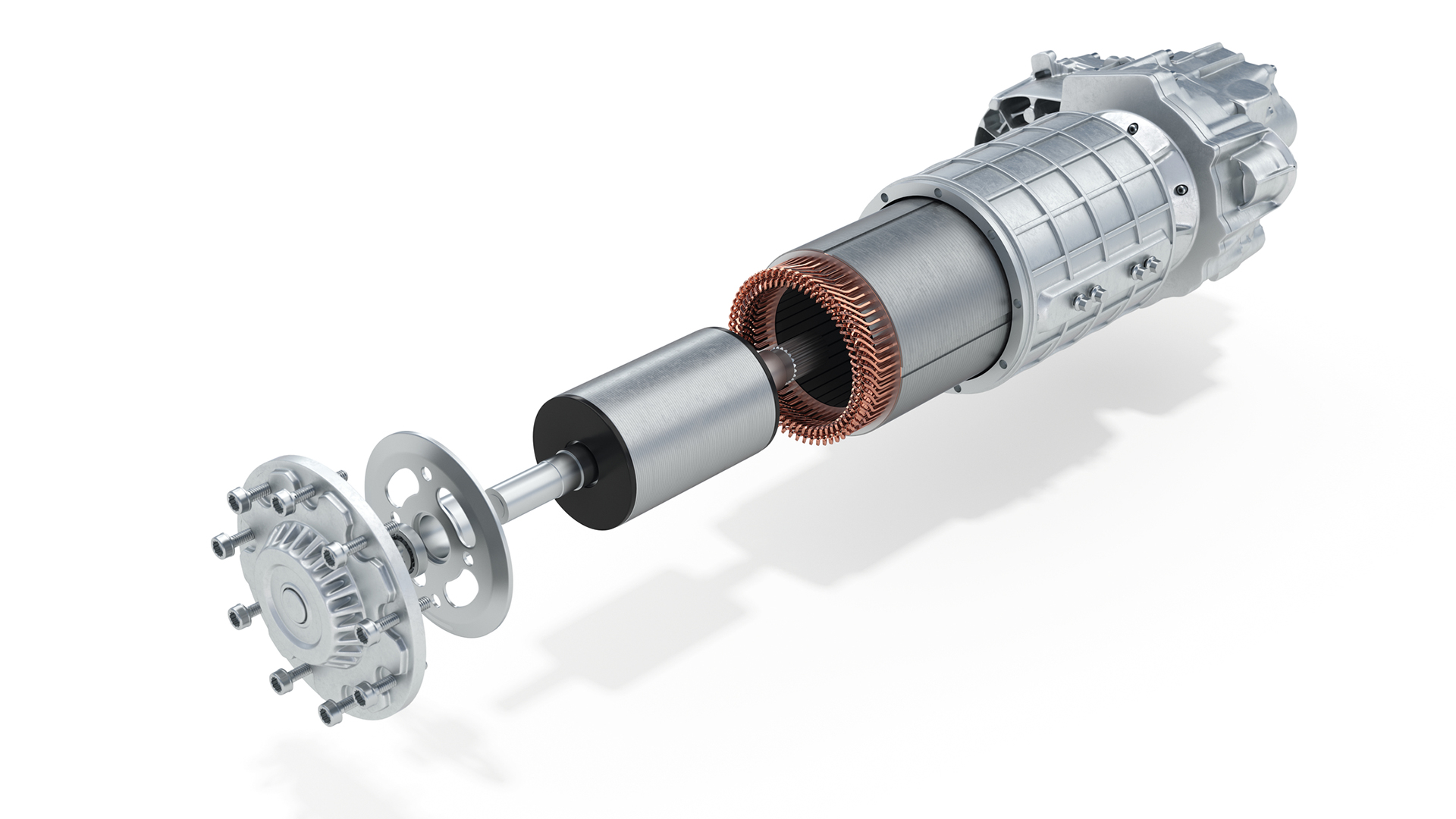
Automated Optical 3D Measurement Technology
Fast, Precise and Reproducible Measuring Results
The ZEISS ATOS Q (EV) blue light 3D scanner is integrated into the automated ZEISS ScanBox for eMotors. The ZEISS ATOS Q (EV) sensor quickly captures accurate 3D measurement data from an electric motor hairpin assembly for fast, reliable, efficient electric vehicle stator inspection. As a non-contact 3D scanner, ATOS Q (EV) captures complete data from objects sensitive to touch, such as EV motor hairpins, allowing you to gain detailed, reproducible measurement results.
|
|
|
Fast and Efficient Full Surface DigitalizationThe ZEISS ScanBox for eMotors is an innovative solution specializing in the full-surface, automated 3D scanning of single or multiple hairpins and complete stators— without surface treatment. Now you can quickly digitize NEV motor components with precision. |
Geometrical Digital Twin of Your EV Motor Components
The software uses the accurate data the ZEISS ScanBox for eMotors collects to generate a complete digital twin. By comparing this digital twin to the CAD model, you can quickly and repeatability identify deviations and defects in the component. |
VMR Compatability for Easy Operation
Program and control the ZEISS ScanBox for eMotors with the Kiosk Interface. This intuitive, user-friendly software lets you get started fast. Simply insert the component, select the measuring program, and press the start button. |
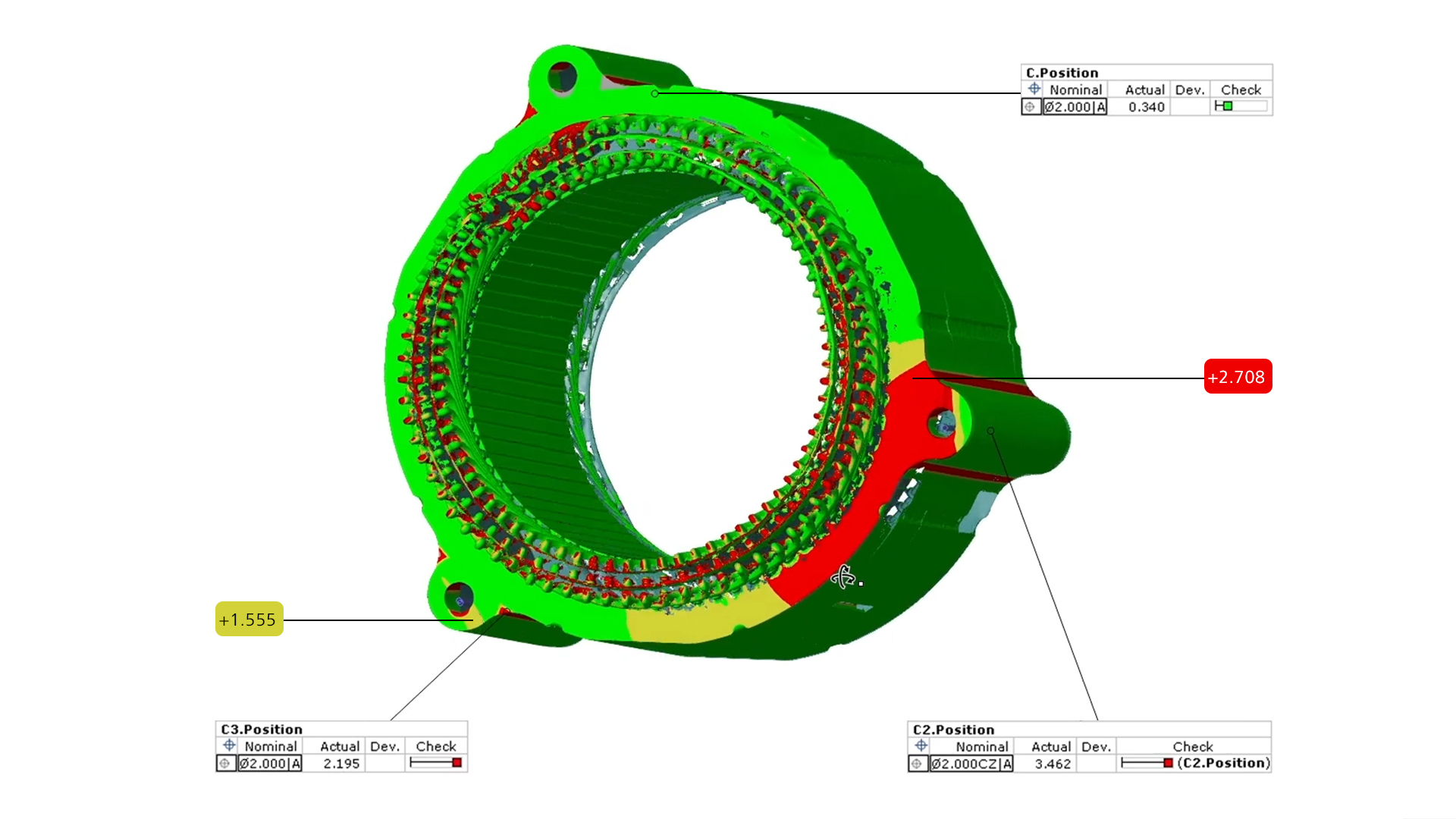
All-in-One Software Solution for Your Entire Workflow
From data acquisition to reporting, you can operate the ZEISS ScanBox for eMotors within the ZEISS Quality Suite. Whether your measurement workflow is simple or complex, you can execute your NEV motor inspections in this single ecosystem— from individual measurements to monitoring in series production. The intuitive Kiosk Interface and the virtual measuring room (VMR) make it easy to run the optimal measurement and inspection sequences to generate an accurate digital twin fast. Typical analyses for hairpin quality control are form, angle, position tolerances, bending points, radii, and leg lengths — all of which can be done inside the inspection software within the ZEISS Quality Suite.
Virtual Measuring RoomInside the ZEISS Quality Suite, you'll find the virtual measuring room (VMR). The VMR contains a functional digital twin of the ZEISS ScanBox for eMotors to support robotic programming, including the kinematics of the robot paths. Smart Teach functions define and simulate the sensor positions. Then the software automatically evaluates and optimizes the program to ensure you're digitizing your part completely. You can traverse and compare positions in the measurement plan with previously imported CAD data or a reference model previously created offline.
Inspection of EV Hairpin Motor StatorsOnce you have your digital twin, you can compare the actual data to the nominal data from the CAD model. For this purpose, the two data sets are aligned, such as the inner cylinder of the sheet metal package, a face, notch or a connecting hole. You can check various quality criteria using a comparison of surfaces. While the inspection of a stator includes checking for cracks, deformations of the winding cage or the connection points, deflections, displacements, and the roundness of the inner cylinder, the focus of the NEV hairpin inspection is on features such as deformations at the hairpin ends or the bending and folding process.
Trend AnalysisAutomatic trend analysis identifies deviations from the design intent early in your process. Continuous measurements quickly detect changes in previous production steps. This data points you to necessary adjustments so you can implement the right changes to previous production steps.
Digital AssemblyThe stator and the rotor in an electric motor must be precisely aligned with each other. You can use digital assembly to verify this critical detail by simulating and checking the component in advance. By using accurate 3D scan data from your ZEISS ScanBox for eMotors, you can use digital assembly to evaluate the fitting accuracy of the components before ever assembling them in the physical world.
|